Les voitures de Formule 1 sont munies de disques et de plaquettes de freins fabriqués dans un matériau composite dont les performances et l’endurance sont réellement stupéfiantes.
Plus léger que l’acier, avec une capacité d’absorption thermique nettement supérieure, le composite carbone/carbone avec lequel on fabrique les freins au carbone des voitures de Formule 1 a été découvert en 1958 à la suite de la pyrolyse accidentelle d’un composite fibreux.
Le freinage miraculeux au carbone est apparu en Formule 1 au début des années 80 sur les Ligier-Matra et les Brabham, mais seulement lors d’essais sporadiques.
Mais après des milliers de kilomètres d’essais et de développement avec la firme française Carbone Industrie, les McLaren-TAG de Niki Lauda et d’Alain Prost s’accaparèrent des deux premières places au championnat du monde de 1984. Depuis, toutes les équipes ont adopté ce freinage et quelques autres compagnies se sont aussi lancées dans la production de ces disques et plaquettes pour la F1.
Les composantes des freins sont longues à produire. « On démarre avec un tissu fibreux blanc de carbone qui ressemble un peu à une barbe de Père Noël, » explique Philippe Rérat, le directeur commercial de Carbone Industrie, filiale de Messier-Bugatti établie à Villeurbanne en banlieue de Lyon en France.
« Ce tissu quasi-isotropique s’appelle Novoltex. On carbonise ce tissu dans un four spécial. Il est ensuite coupé dans la forme rudimentaire de la pièce à produire, que ce soit un disque de freins ou une plaquette, » de poursuivre Rérat à Auto123.com.
« Puis, on passe à l’étape de la densification dans des fours d’infiltration. Grâce à un procédé de craquage d’hydrocarbones à 1 000 degrés, une matrice de pyrocarbone se mélange parfaitement au Novoltex, » explique Rérat.
« Le morceau se densifie, c’est-à-dire qu’il devient plus compact, que les cavités situées à l’intérieur se remplissent complètement. C’est un procédé très long, qui dure de longues semaines. Finalement, on usine la pièce à des cotes précises. Il faut compter plus de cinq mois de travail pour fabriquer un jeu de freins. Auparavant, il fallait près de six mois, mais nous avons réduit le temps d’intercycle. »
Les pièces de frein en carbone sont cinq fois plus légères que des composantes identiques fabriquées en acier. De plus, les disques en carbone sont insensibles aux chocs thermiques, possèdent des caractéristiques mécaniques qui augmentent avec la chaleur -- ce qui est l’inverse de l’acier traditionnel -- et peuvent encaisser des températures allant jusqu’à 1 000 degrés.
Ces disques s’usent lentement et résistent aux oxydations allant jusqu’à 500 degrés. Le coefficient de friction du carbone est très élevé et permet à une voiture de F1 de ralentir de 320 à 100 km/h en 120 mètres ou trois secondes. Assez pour faire sortir vos yeux de leurs orbites!
Le coefficient de friction varie peu, même à des chaleurs extrêmement élevées.
Et contrairement à ce que colporte la légende urbaine, même froids, les freins au carbone répondent quand même bien.
photo:Matthieu Lambert - Auto123.com
Plus léger que l’acier, avec une capacité d’absorption thermique nettement supérieure, le composite carbone/carbone avec lequel on fabrique les freins au carbone des voitures de Formule 1 a été découvert en 1958 à la suite de la pyrolyse accidentelle d’un composite fibreux.
![]() |
Les disques et plaquettes rougissent lors des freinages. Photo: WRI2 |
Le freinage miraculeux au carbone est apparu en Formule 1 au début des années 80 sur les Ligier-Matra et les Brabham, mais seulement lors d’essais sporadiques.
Mais après des milliers de kilomètres d’essais et de développement avec la firme française Carbone Industrie, les McLaren-TAG de Niki Lauda et d’Alain Prost s’accaparèrent des deux premières places au championnat du monde de 1984. Depuis, toutes les équipes ont adopté ce freinage et quelques autres compagnies se sont aussi lancées dans la production de ces disques et plaquettes pour la F1.
Les composantes des freins sont longues à produire. « On démarre avec un tissu fibreux blanc de carbone qui ressemble un peu à une barbe de Père Noël, » explique Philippe Rérat, le directeur commercial de Carbone Industrie, filiale de Messier-Bugatti établie à Villeurbanne en banlieue de Lyon en France.
![]() |
Disque de freins carbone de F1. Photo: Matthieu Lambert Auto123.com |
« Ce tissu quasi-isotropique s’appelle Novoltex. On carbonise ce tissu dans un four spécial. Il est ensuite coupé dans la forme rudimentaire de la pièce à produire, que ce soit un disque de freins ou une plaquette, » de poursuivre Rérat à Auto123.com.
« Puis, on passe à l’étape de la densification dans des fours d’infiltration. Grâce à un procédé de craquage d’hydrocarbones à 1 000 degrés, une matrice de pyrocarbone se mélange parfaitement au Novoltex, » explique Rérat.
« Le morceau se densifie, c’est-à-dire qu’il devient plus compact, que les cavités situées à l’intérieur se remplissent complètement. C’est un procédé très long, qui dure de longues semaines. Finalement, on usine la pièce à des cotes précises. Il faut compter plus de cinq mois de travail pour fabriquer un jeu de freins. Auparavant, il fallait près de six mois, mais nous avons réduit le temps d’intercycle. »
Les pièces de frein en carbone sont cinq fois plus légères que des composantes identiques fabriquées en acier. De plus, les disques en carbone sont insensibles aux chocs thermiques, possèdent des caractéristiques mécaniques qui augmentent avec la chaleur -- ce qui est l’inverse de l’acier traditionnel -- et peuvent encaisser des températures allant jusqu’à 1 000 degrés.
Ces disques s’usent lentement et résistent aux oxydations allant jusqu’à 500 degrés. Le coefficient de friction du carbone est très élevé et permet à une voiture de F1 de ralentir de 320 à 100 km/h en 120 mètres ou trois secondes. Assez pour faire sortir vos yeux de leurs orbites!
Le coefficient de friction varie peu, même à des chaleurs extrêmement élevées.
Et contrairement à ce que colporte la légende urbaine, même froids, les freins au carbone répondent quand même bien.
photo:Matthieu Lambert - Auto123.com
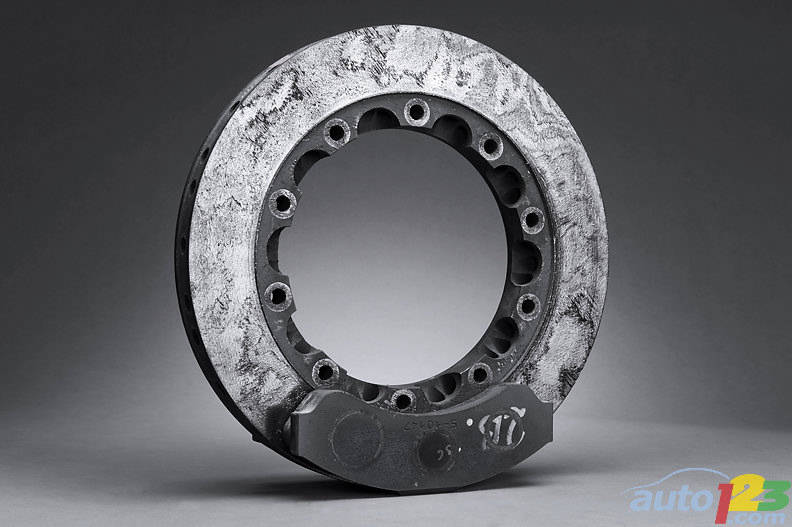
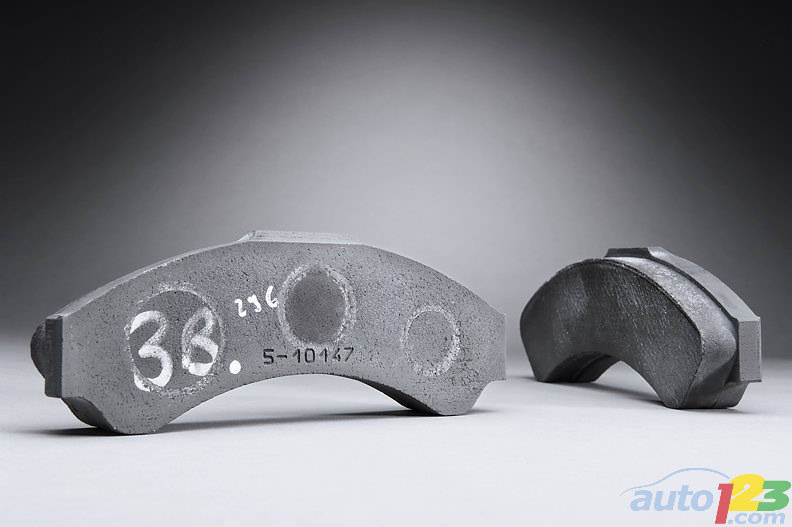
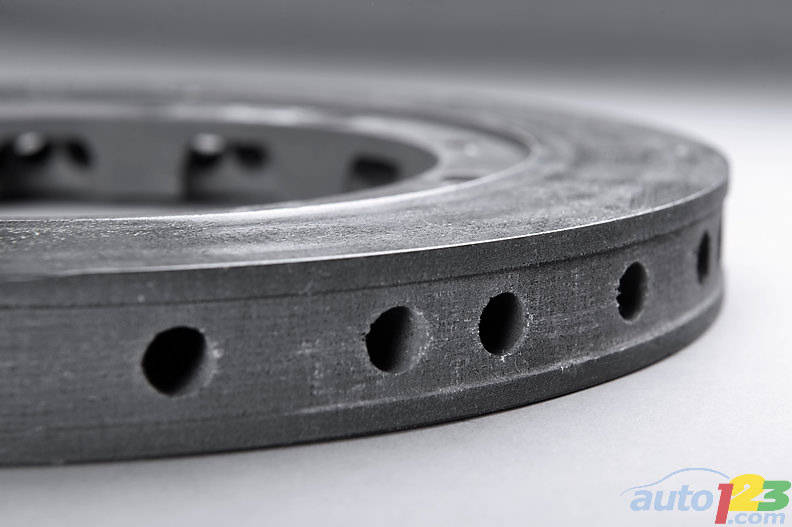
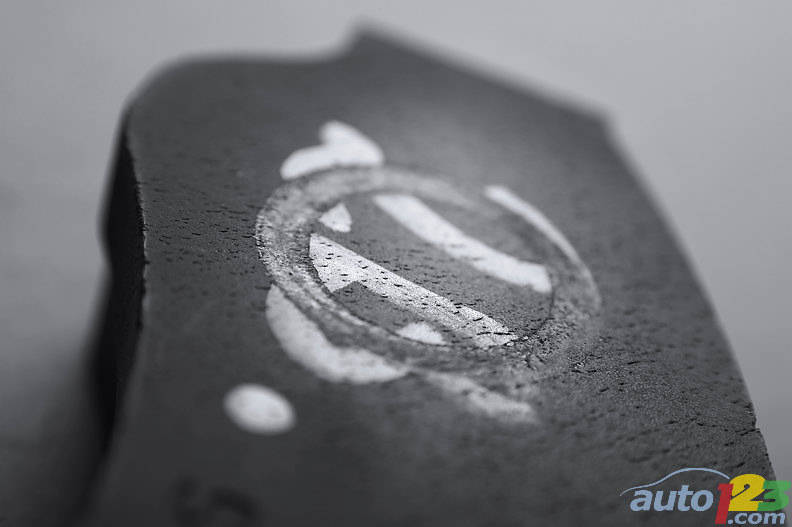
Gallerie de l'article