Be honest now: What comes to mind when you think of what it must be like working on the assembly line at an automotive plant?
“Oh my God, It must be deadly boring!,” exclaimed my better half when I asked her the question. “Repeating the same gestures over and over!”
I’d wager that’s pretty much the answer you’re going to get 9 times out of 10. It’s what I answered to myself. When the invitation to visit Toyota’s plant in Cambridge, Ontario arrived in the Auto123 mailbox, I jumped on the occasion to head down there and have my preconceived notions confirmed. Nothing like being proven right…
Follow the guide
Toyota has two assembly plants in Canada, both of them in Ontario. Aside from the facility in Cambridge, which was inaugurated in 1986 and for many years produced Corollas, Matrixes and Solaras but is now used to build the Lexus RX 350/450h and RAV4 (both regular and hybrid), a second plant has been in operation in Woodstock since 2005 (it also produces the RAV4, a very popular model indeed in the Great White North).
From the perspective of Toyota representatives, the two Toyota plants are mostly considered as one. In general they refer to them interchangeably as Toyota Motor Manufacturing Canada, or TMMC for short. They leave it up to you to figure out which one is being referred to at any one point, the jokers.
And so when they provide a stat like, say, 497,354 vehicles produced at the TMMC, it takes a little digging to discern that of that total, precisely 97,012 were RXs (15,183 of them the 450h).
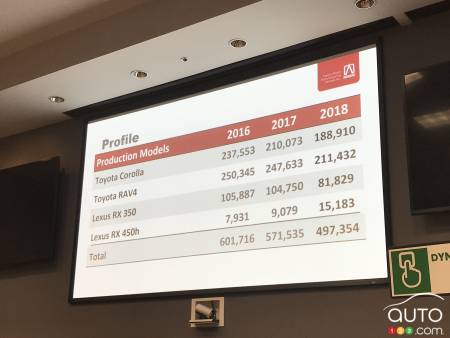
The invitation promised an intimate, exclusive visit. Being aware that the local Chamber of Commerce has been organizing free visits of TMMC since 1998, I became quite curious about the precise meaning of “intimate” and “exclusive”.
But I was quickly reassured by Scott MacKenzie, Senior National Manager of External Affairs for TMMC and Toyota Canada, that he had devised for my colleagues and myself a unique, "behind the scenes" visit.
So like a kid at Disney I sat down with excitement on the bench seat of an electric tram of the sort you see bringing children to see Santa at the mall. The headphones in my ears fed me explanations from our guide about the sections of the RAV4 and Lexus RX assembly zones, both of which wind their way through the facility under the same massive roof.
Massive might be an understatement. Car factories are humongous! The Cambridge facility covers 3.5 million sq ft, enough to swallow up 25 Costco stores. I could melt your brains with an onslaught of statistics but I’ll stick to these: some 8,000 workers (Toyota calls them Team Members) are employed at the Cambridge and Woodstock plants, while Toyota’s investments in the two facilities totals $8.2 billion to date.
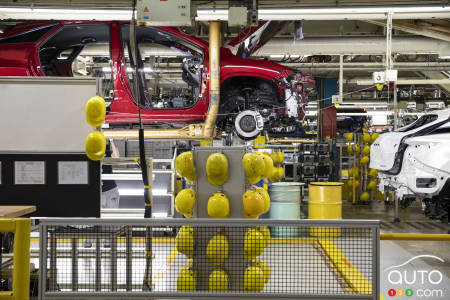
Automation isn’t the whole story
Sure, you see robots at TMMC. Of all sizes. The biggest ones are nicknamed Godzilla, and they would look right at home on the set of a James Cameron epic. Beneath them, small self-driving vehicles called Ottos criss-cross the immense factory floor, transporting parts from one work area to another, with never a collision.
I saw one stop its journey to kindly allow our guide to finish his little speech before once again moving on its way once our convoy of visitors finally got out of its way.
Aside from the robots, I also met Steve MacNeil, General Manager of Lexus Manufacturing. He is so versed in the secret sauce used by Toyota in its manufacturing process that his bosses sent him on a five-stint to Kentucky, where the Lexus ES is built, so he could duplicate there the quality of construction that prevails at the Cambridge plant.
With 32 years of experience under his belt, Steve is clear and adamant about what works: “It’s not just the quality of materials, the right tools and the very specific procedures that guarantee the quality of our work. It’s also due to our Team Members, in particular their level of concentration and their ability to memorize.”
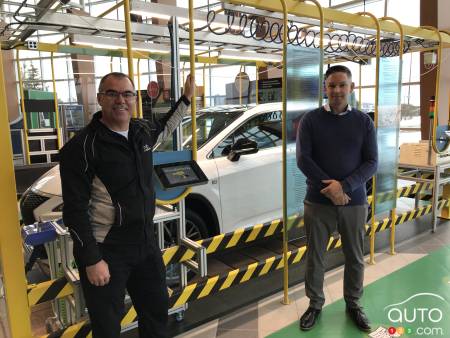
To demonstrate the correctness of his claim, Steve showed us the kind of “games and tests” apprentices must master before being given a job on the line. For example, can you create a cat-shaped origami within 90 seconds, using your non-dominant hand? The best workers – I mean Team Members – at TMMC can.
They can also, with a gloved hand (to prevent cuts), verify that the gap between the car door and the body is no more than 0.3 mm, about the thickness of three sheets of paper. And they can, glove still on hand, caress a piece of sheet metal and detect any imperfections, in four seconds. Even using my bare hand and when I knew exactly where the imperfections were, I felt absolutely nothing…
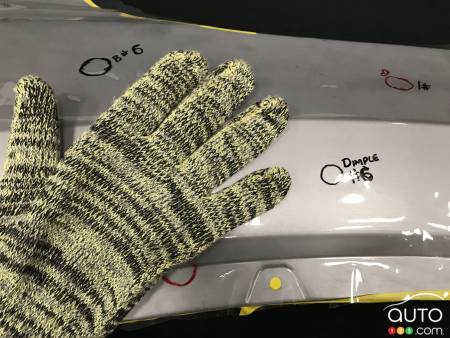
Then there’s the ability to notice small colour differences. I was given four platelets, only one of which had the correct silver tint on it. To me, the four samples looked exactly the same.
Hours and hours of practice awaits new Team Members, clearly. By the time they master most of those tasks, they are generally not even referred to as workers or employees or even Team Members any more, but as “takumi”, which designates an artisan at the top of his art. When the company’s engineers endeavour to create a robot, their goal is to endow it with the perfectionism of a takumi.
What, you may ask, about the deadening routine resulting from doing the same repetitive task all day long?
First of all, before one is a full-time Team Member at TMMC, one is a contract worker (at an hourly wage starting at around $20), so that one can confirm if factory work is really up one’s alley, so to speak. This is not because the work is monotonous, mind you, rather it’s because it’s very challenging, as we’ve seen.
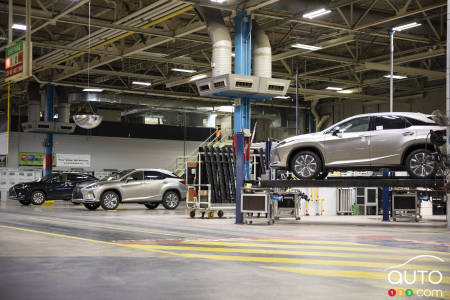
That said, to break up the routine that does exist to some extent, eight-hour work shifts are divided into four two-hour blocs, each one devoted to a different task. The more experienced workers become, the more tasks they master, and the less boredom has the chance to rear its ugly head.
And elsewhere?
As I was absorbing what Scott and Steve had told me, my thoughts turned to the Tesla plant in California – you know, the one that regularly makes headlines for the production screw-ups that occur there. Head honcho Elon Musk can set any production target he likes, the factory rarely meets them. Why? Speaking strictly for himself personally, Scott MacKenzie believes there are too many robots and not enough humans to supervise and repair them.
He didn’t add, but could have, that the humans that are on hand there do not benefit from the experience that decades of trial and error bestow. In other words, it’s pretty darn difficult to improvise your way into being a car manufacturer virtually overnight (which Tesla has done, with remarkable success it must be said).
“Toyota works step-by-step to arrive at the stated goal. It takes us more time to bring production capacity from 94% to 96% than it takes Tesla to go from 30% to 100%.”
- Scott MacKenzie, Toyota/Lexus
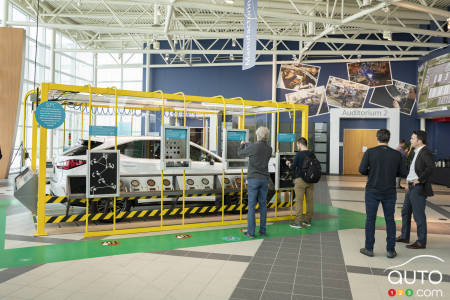
Let’s take German brands, then. We media hacks are the first to laud the engineering, designs and performances of their vehicles, but in the next breath we cast doubt on their reliability. Should we point the finger at the factories that make them?
Kid gloves still firmly on hands, Scott says, “I would look more at the parts provided by suppliers. In the case of the RX, for example, 80% of its components come from external suppliers. But everyone works hand in hand.”
Every part of a vehicle has a head designer, who supervises other designers who are in turn in charge of the different parts that make up, say, the dashboard. Once the design of a part is settled on, the company asks for submissions from suppliers able to deliver a high-quality part within budget.
It takes 11.6 hours to paint an RX to everyone’s satisfaction. Those who work in the paint studio take air showers to eliminate impurities on their clothes. Even in a facility in which gigantic Komatsu presses work non-stop to shape sheet metal, the factory is well-lit, airy and so clean you could picnic on the floor.
Every vehicle undergoes 4,877 quality tests before leaving the factory.
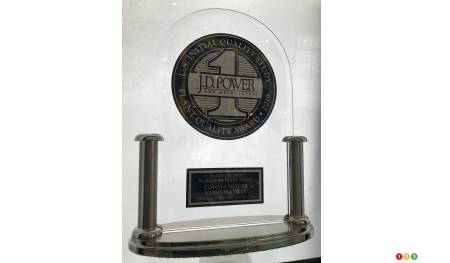
No surprise then to learn that the Cambridge plant is regularly ranked first in class. Up until now it has won a pile of awards recognizing the excellence of its products, including 18 given by J.D. Power, the American firm that specializes in providing and analyzing statistics and conducting surveys. It doles out awards to various players in the automotive domain at the pace of a single-minded egg-laying chicken.
In fact, the 18 J.D. Power prizes the factory has earned places it only one behind the world champion in this regard, the Kyûshû plant in Japan. And what does that facility produce? Why RXs, of course!
Last point I should note: there is no union at TMMC – yet more evidence that the work environment there can’t be that bad. When unions obtain something from the American Big Three, the Japanese give it, if it hasn’t already been given.
Cambridge is a shining star in its field; to wit, it was the first non-Japanese plant to be given the right to build Lexus vehicles. Starting in 2022, it will also build the NX compact SUV. Which means that the top two best-selling Lexus models in North America will be “Made in Canada”.
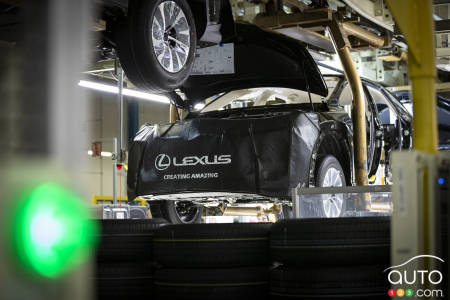
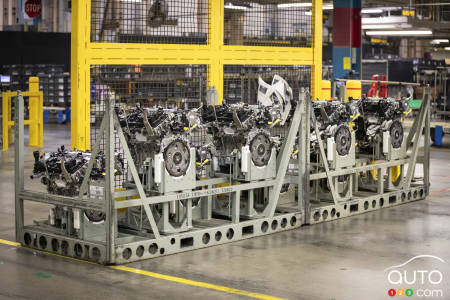
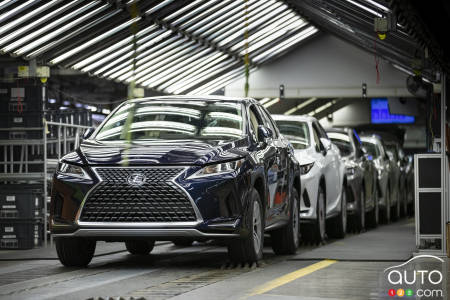